Aprendo la strada ad un nuovo livello di applicazioni nell’Industria 4.0/Iot, Denso Robotics ed i suoi partnerhanno recentemente mostrato come l’automazione industriale nelle “smart factories“ possa essere ancora più efficiente, sicura ed affidabile,utilizzando al meglio i software e le tecnologie già esistenti. Al centro della dimostrazione del progetto “Deniot”, è stato utilizzato il robot Denso VS060 e la piattaforma cloud Azure di Microsoft, una raccolta di servizi cloud integrati come: elaborazione dati, database, mobile, networking, archiviazione dati e website. La dimostrazione si è svolta presso l’importantissima .Net Conference di Microsoft a Madrid, in Spagna. Si è dimostrato che le performance dei robot possono essere notevolmente ottimizzate sfruttando tutti i vantaggi di una piattaforma cloud, come quelli offerti da Azure. La piattaforma è stata connessa al controller del robot Denso per raccogliere ed analizzare i dati, utilizzando Big data analytics e altre tecniche. Questi dati sono stati poi trasformati in informazioni operative. Nella dimostrazione, il robot VS060 è stato programmato per eseguire fino a 9 movimenti diversi, soprattutto di pick-and-place. “Il nostro obiettivo era quello di dimostrare come sia possibile ottimizzare le performance del robot utilizzando le tecnologie ed i processi già esistenti. Osservando ed analizzando i dati del robot, non solo siamo in grado di interagire con esso e controllarlo da qualsiasi luogo, ma abbiamo inoltre semplificato l’apprendimento automatico, il quale migliora ulteriormente l’efficienza e le performance,” afferma Pablo Olivares. I robot Denso sono particolarmente adatti per le applicazioni di Industria 4.0/Iot dal momento che il Controller RC8 è altamente flessibile e semplice da integrare. Questo è fondamentale, visto che la chiave di ogni soluzione Iot di successo è rappresenta da una coordinamento semplice, rapido ed affidabile di tutte le parti che compongono il sistema. Ci sono molte piattaforme con cui il controller Denso RC8 può lavorare, tra cui LabView, Halcon o Plc Industrial network (es. ProfiNet, ProfiBus, ecc.). Per il progetto “Deniot”, Orin è stato il più importante. Orin (Open resource interface for the network) un’interfaccia di sviluppo software, che permette di interagire con robot ad elevati livelli di linguaggio come C#, C++, ecc. Questa unica capacità di programmazione permette l’integrazione molto semplice delle piattaforme software tra il robot Denso e Microsoft Azure. Durante la dimostrazione, il robot è stato controllato anche attraverso l’utilizzo di Cortana, il software di assistenza e riconoscimento vocale sviluppato da Microsoft. Tra tutti i movimenti eseguiti dal robot VS060, l’ultimo è stato quello che ha riscosso più successo tra il pubblico, ossia: il robot che si fa un selfie.
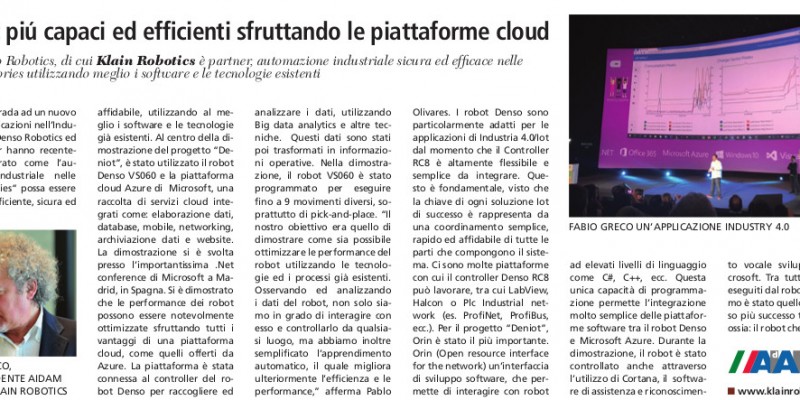